Building IMOCA 60 11.2 Part 3: The Build Story
Guest author Mark Chisnell provides a three-part series diving into the details of our new IMOCA 60 11.2. In part one, he explores the multiple challenges our team faced when building the boat. In part two, he explains how these issues were solved through a sophisticated design.
In the third and final part, he gives detailed insights to the boat building process and different components on the first IMOCA 60 designed for crewed sailing in The Ocean Race.
11th Hour Racing Team’s new IMOCA 60 – known as 11.2 – rolled out of the build shed at CDK Technologies in Port la Forêt, France, on August 9, 2021. Both 11th Hour Racing Team’s skipper, Charlie Enright (USA) and the naval architect Guillaume Verdier (FRA) acknowledged that reliability was the short-term priority: if the boat is not reliable it’s not going to win anything. And this boat is different to all previous IMOCA 60s: it was purpose-built to be sailed fully-crewed. The structural design assumed higher hull pressure loads in the slamming zones, so one of the first objectives will be to measure the loads that the boat’s experiencing as it’s pushed hard in tough conditions.
Slammin’ hull technologies
Naval architect Guillaume Verdier has a background in structural engineering and has always been cautious about slamming. His approach this time was no different to his previous boats.
“I decided some time ago to use a single skin [of carbon fibre] on the bottom [of the hull], even at the Group Finot design office, we were single skin. If you think about it, when you have a sandwich, if you need to make it very strong, you end up making a very heavy sandwich. When you are 100% dependent on the core to skin attachment, that’s very scary, I find, in the slamming zone. I prefer to make a structure which is actually lighter with little ribs and a single skin. It’s also quite forgiving, because if you break a rib but you don’t break the skin, you can always fix it. If you debond the core, you’ve got no other choice than stopping. It’s quite a pain to build and it makes for a complex structure, but it’s very resilient and that’s a choice I’ve made right from the beginning.”
This was just one aspect of the complex manufacturing process for the new boat. The team chose CDK Technologies to achieve the build quality that they required. It’s a company with 35 years’ experience of building boats for the elite offshore racing market, including the last four winners of the Vendée Globe and the largest racing trimaran ever built, the Maxi Banque Populaire V. The team were buying into an established set of composite construction techniques using female molds with prepreg carbon. There is no escaping the fact that building an IMOCA 60 sailboat requires both energy and materials; thermal and chemical energy is absorbed into the bonds of the carbon resin matrix to make the material strong. However, it was also vital to the team’s goals – as an advocate of sustainable futures in the marine environment – that the material, energy use, and the waste in the process was kept to an absolute minimum. While a lot of the materials were determined by the IMOCA Class Rules and the technical preferences and experience of CDK Technologies, the latter were both open and willing to participate in a review of the whole of their manufacturing process, and IMOCA have now introduced rules to encourage sustainable build programs.
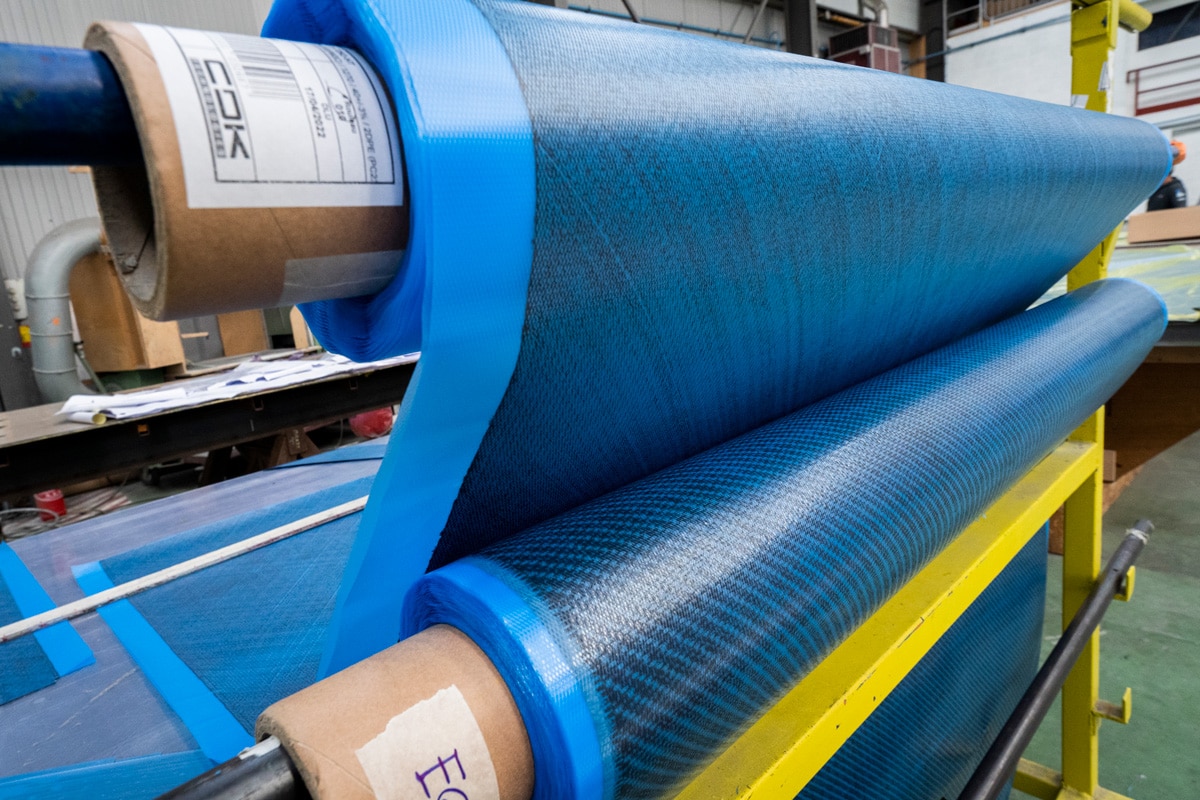
Sustainability from the start
Amy Munro is 11th Hour Racing Team’s Sustainability Officer, and she explained,
“It was really key to start exploring right at the beginning what the opportunities would be with the relatively short timescales that we had. So, we started off by creating a working group, with the intention of trying to embed circular economy principles throughout the process right at the beginning. But also, to understand what we could test, what we could embed and include within our processes and what we could recommend for future builds as well.
“So, the working group involved our designers, the builders [CDK Technologies] and the sailors and we’d run the meetings every six months. It involved exploring new materials and looking at how we could work with the IMOCA Class on new sustainability rules that would incentivize change quicker. And working out where the big impact hotspots were and concentrating some time and effort in those spaces. We got some really good suggestions and projects that we explored as a result of that work, and many have ended up as exciting features on the boat.”
“The work that the Team is carrying out is really the first step in identifying how we can do things differently, with sustainability as a core principle but maintaining the high-performance needs that are required by the sport of competitive sailing,” explained Jeremy Pochman, co-founder and CEO of the Team’s sponsor, 11th Hour Racing. “The Team executed a full Life Cycle Assessment (LCA) of the build of 11.2 in order to determine the environmental impact of the different components and procedures – building on a previous study done by Kairos in 2010. This will help the team establish a new benchmark and provide an understanding of how the IMOCAs have changed in the last ten years, and what needs to be done going forward.”
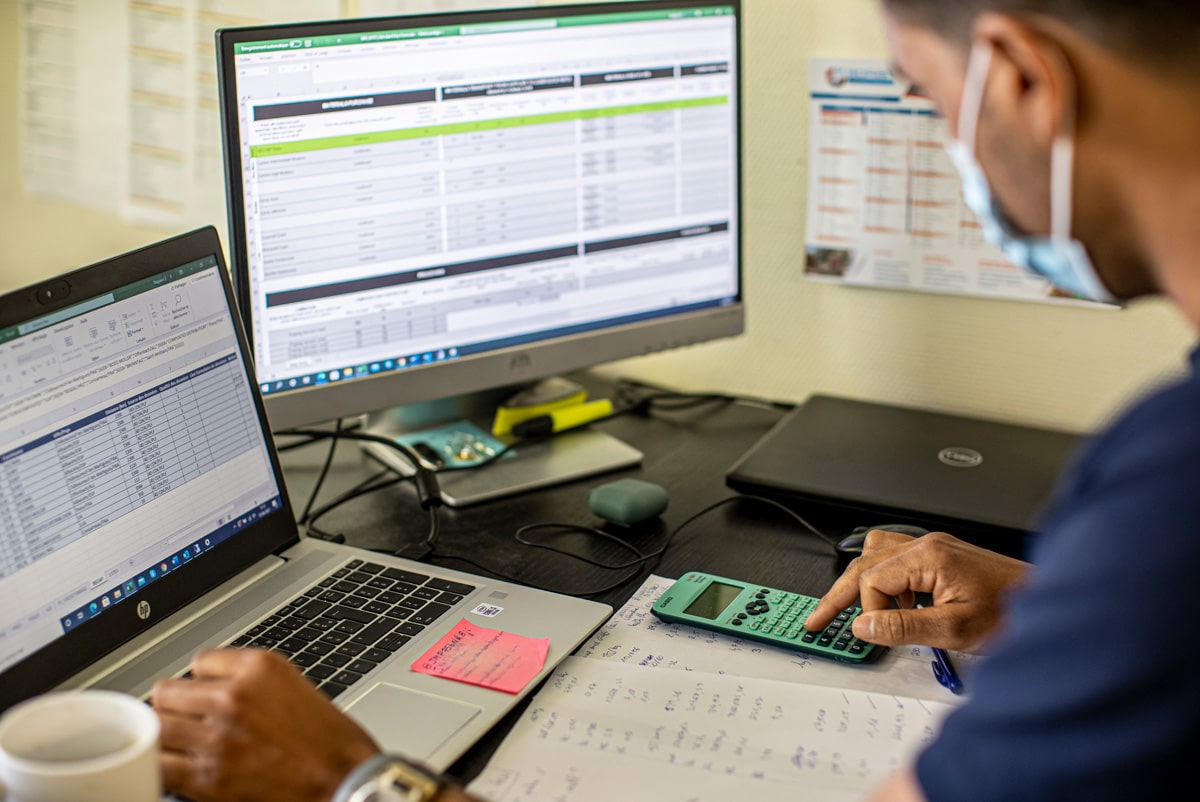
Easy wins
“We believe that if you can’t measure it, you can’t manage it,” Amy Munro said of the Life Cycle Assessment. “So really understanding the full picture of the build, looking at everything from the sourcing of the materials to the transport, the design, build, manufacturing, use and end-of-life phases and understanding all the materials and processes. Where are the big impact hotspots so that we can concentrate our recommendations and our actions in those spaces?
“One thing that CDK did that’s a really easy win is that they’re on a hundred percent renewable energy tariff. About a third of the footprint of the build is energy use in the construction facility, autoclaves, power and lighting,” continued Munro. “So, because they’re on renewables, that brings it down by 30%. That’s a great starting point that every boat manufacturer can look to do really easily, depending on where you are and what you’ve got available. Not only does this increase demand for renewables, it will also significantly reduce your manufacturing impacts.”
Jeremy Pochman added,
“Change comes not only from innovation but also from implementing better everyday practices around waste management and energy consumption. Waste and energy contribute massively to the environmental impact of the marine industry, and while they can be labeled as the ‘low hanging fruit’, they are part of an overall need to make the industry more sustainable as a whole.”
“CDK Technologies have some great waste management processes set up with really quite high levels of recycling and great relationships with their suppliers,” said Munro. “So one example, as a result of the environmental audit that we did with them, was that they started to work with their carbon fiber suppliers and returned all of the packaging at the end of each period. This resulted in a financial saving of nearly five thousand Euros, reducing one thousand kilograms of cardboard waste and preventing one tonne of CO2e emissions per year. CDK Technologies are also looking at their autoclaves and using a closed water system so that there’s no water wasted, along with various other efficiencies across the board like insulation in the roof.”
Another easy, yet significant win was the mold used for the construction of the boat. “It’s going to be reused by another team, which is great,” said Munro. The boat will be for Yannick Bestaven and his commercial partner Maitre CoQ and will also be built at the CDK Technologies yard in Port-la-Forêt. “This is really efficient, the mold didn’t even leave the autoclave and CDK has already started a new build with the same component. Bestaven’s team is ultimately receiving an impact-free mold because we’ve already taken these into account in our footprint calculations and offset it under our project. As the hull and deck molds represent close to 50% of the impact of an IMOCA as built, this could almost halve the impact of their build. We’re hoping that it can be used for a third boat as well, which would be great to see, and really underlines the importance of reuse.” Putting this into context, Munro explains, “While we must work on seeking out better materials and alternative processes, designing for reuse and longevity is direct, relatively easy, and can provide the immediate impact reductions at the scale we need.”
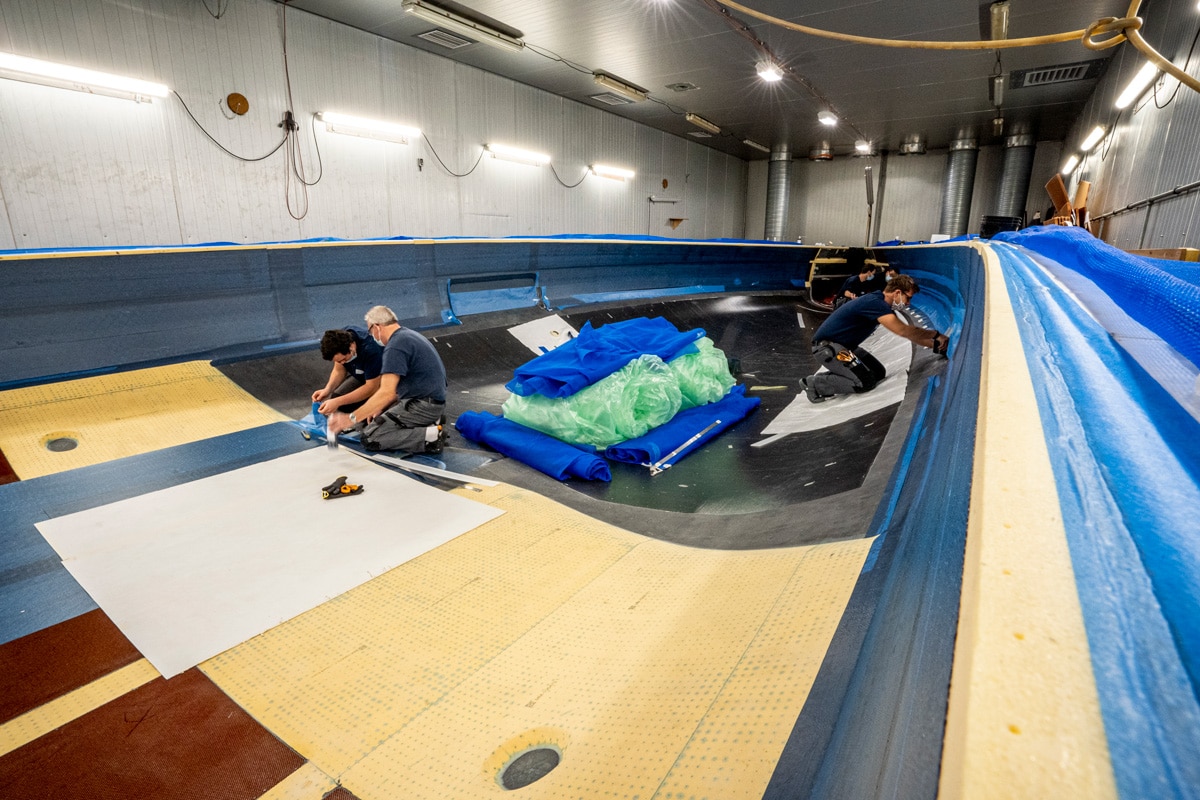
powerRibs and rPET core
The team also made progress in the materials they used.
“I think materials innovation is exciting, looking at how we can do things with a different approach, particularly at the design stage because around 80% of the impact of your build is locked in at design. There is only 20% that you can have an impact on after that’s done,” explained Munro. “We have used a product called powerRibs, a natural flax fibre reinforcement mesh that mimics a leaf vein structure. So, it uses less material for its strength, and also acts as a transfer medium for the resins.”
A lot of the research and materials testing was led by the team’s Build Manager, Wade Morgan. “The IMOCA Class brought in a new rule for the use of alternative materials up to 100 kilos, and that’s a big deal because we can build a lot of furniture components and try some new materials and techniques. We’re at about 60 kilos on the boat now, that’s over 80 square meters of flax fiber going into the boat. We’re also using recycled PET core [polyethylene terephthalate or PET is used in plastic bottles, and is now recycled into a core material used in composite ‘sandwich’ constructions] and we learned a few lessons on best practice and application.
“The trickle down impact, the places where this knowledge that we have learnt can be shared and where we can really make a significant difference is not in the grand prix market though, it’s in the far larger cruising boats, or powerboat market,” explained Wade Morgan. “So I’m really looking forward to collaborating with as many IMOCA teams and other grand prix teams that have the ability to test these products as I can, and hopefully we can come up with guidelines and methods for these materials to give to other builders that maybe don’t have the economic ability to try them. As a small boat builder, experimenting is not something that typically you can afford to do, so hopefully our learnings can help in that area.”
3D gains in 3D printing
An area where the Team has seen performance, economic and environmental gains is in the use of 3D printing in plastic and metal.
Wade Morgan again, “3D printing is a thing that’s coming online more and more… 3D printing titanium, 3D printing plastic for jigs. Something like a drilling jig, for example, historically you’d machine something large, whereas now we can do a very hollow plastic part that we can print, and we don’t make mistakes. That’s the biggest thing for me… if we are able to get something right the first time by using the complex 3D software and having good references on each part we limit man hours and we get a more efficient build; both from a carbon footprint and an economic side of things… It could be a little cover for a vent or a drain in your daggerboard case, you’ll just print a little part and it will be ready to go. Or it could be your trip-line organizer. Instead of building a carbon part and turning it into dust to make all the grooves – and you think about the time and the wastage and the labor that goes into that – now you design it in 3D and then you don’t waste anything and those good quality plastic parts go straight on the boat…
“We’ve been quite aggressively going down that path saying, ‘Is this a job for a person to sit there and build from scratch, or is this a part where we should print a mold, CNC something, scan something from a 3D aspect?’ So even our foils, I think it’s pretty standard, but our foils get scanned before our bearings get cut so that we know the exact surface of them. So, the digital side of it is something that is moving into this offshore sailing world, it was almost exclusively for America’s Cup and Formula 1, but it’s becoming more commonplace nowadays.”
Supply chain
There are also gains to be made in the supply chain. “The more you talk to suppliers and put that request out there, then the quicker they’re going to move,” said Amy Munro. “We’ve got to get to a 50% overall reduction in greenhouse gas emissions by 2030 and net zero by 2050. So, we’re only going to be able to do that with real collaboration and making sure that we’re working in targeted areas and working together.” Munro pointed to line and cordage manufacturer Marlow as an example. They are supplying a bio-based Dyneema to the Team that they feel has “identical technical characteristics and performance as conventional Dyneema but uses waste from the pulp and timber industry as its primary raw-material. “More than 50 suppliers are engaged on this topic now across our build alone, which is a really big win as well. Making positive sustainable sourcing choices is one of the most effective actions that we can be taking as consumers to reduce our footprint,” commented Munro.
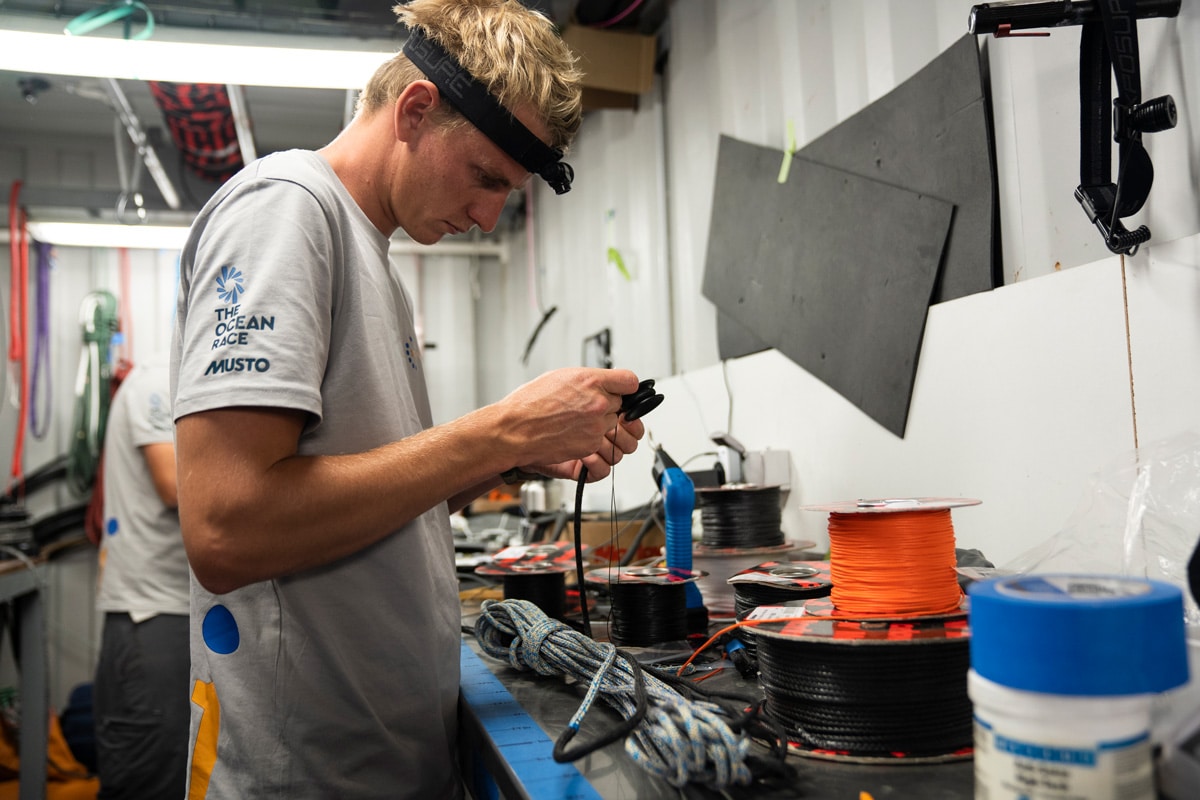
Challenges and opportunities
There are still many challenges though, not least of which is what to do with the boats when they reach the end of their life.
“The first thing we need to do is design for a long use, and multiple campaigns,” said Munro. “So, a long use-phase is the first part… And as carbon fiber recycling is becoming more and more viable, making sure that we recycle the carbon at the end of its life from not just the molds, but from the boat itself.”
Recycling carbon fiber has proved to be a difficult technical problem, but there is some interesting progress being made by Lineat Composites based out of the University of Bristol, in the United Kingdom, who have developed a technology to better reclaim chopped carbon fibers by using waterjet technology to align the material in tapes to achieve mechanical performance comparable to continuous fiber composites. This is a significant step forward from the current end product of carbon recycling – a resin-thirsty chopped strand mat. “They have taken one of our broken foils,” explained Munro, “they’ve recycled it, recovered the carbon from the foils. And then they’re realigning the fibers and turning that into a tape that they’re going to give back to us to use to build future components on board. This is the circular economy in action.
“For us as the team, it’s about showing leadership by example,” concluded Munro. “So not just speaking about it but making sure that we’re really embedding it across the whole team and working in ways that are replicable by other teams and organizations and then sharing this knowledge. Earlier this year we launched The Sustainability Toolbox, which is a whole set of how-to guides, case studies, and tools, templates, practical resources for other teams, events, organizations or businesses – whatever their industry – to be able to run their own sustainability programs in-house, without any particular sustainability expertise.”
The Sustainability Toolbox has been downloaded and elements implemented by a broad range of organizations from sports teams to events, financial services companies to service providers.
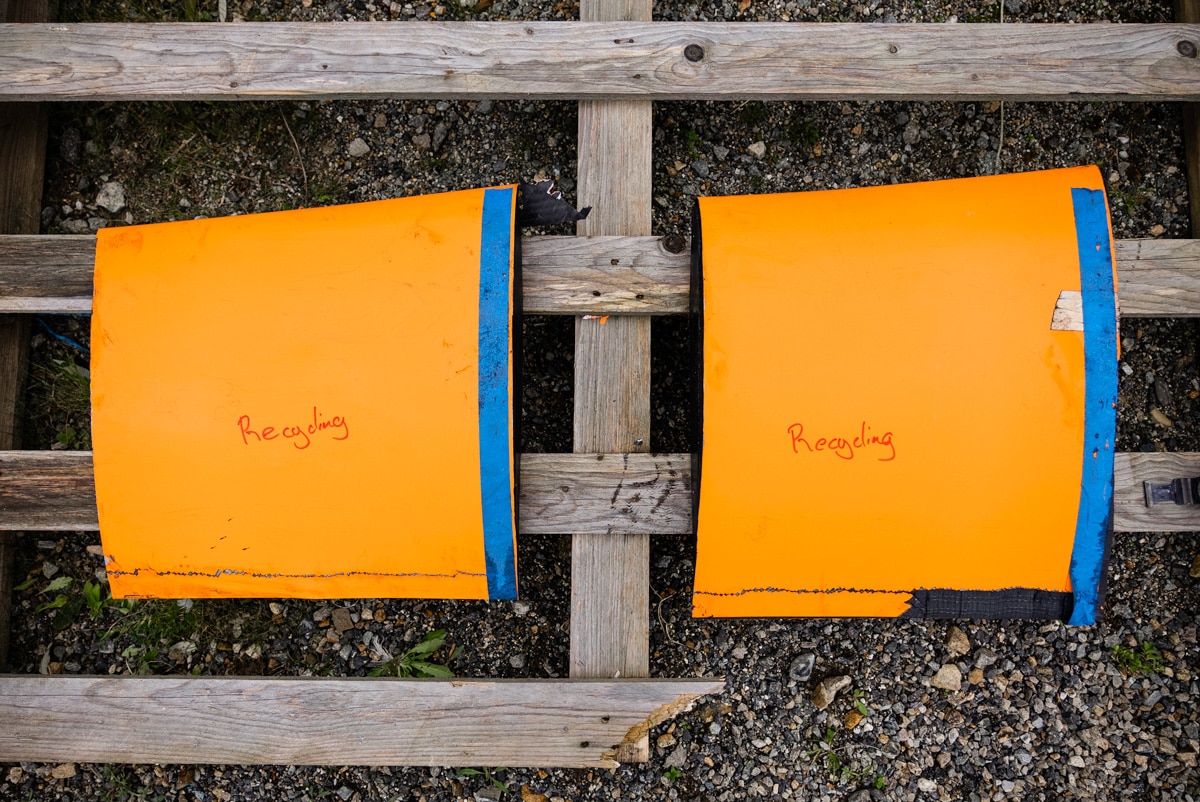
Mark Towill, CEO of 11th Hour Racing Team, is happy with the progress and the legacy of the sailing team. When I asked him what was the most important aspect of the innovation and the technology that has been developed in 11th Hour Racing Team’s program he was clear.
“I think it’s everything we’ve done on the sustainability side, the boat building practices, the LCA tool; all of this is applicable to everybody that’s building a boat today. Is everybody that’s building a boat today going to foil around? No, but the renewable materials, the reduction in waste; all of this knowledge that we are sharing can be used by other manufacturers and can be demanded by people and teams looking to build their own boats. Thanks to the support we have from 11th Hour Racing, we’re in a position where we can be experimenting and taking the chances that other people might not have the opportunity to take, and then sharing the results and trying to get more people engaged with it. Hopefully that is our biggest trickle down and the biggest, positive impact we will have.”
Jeremy Pochman concluded,
“We need innovation in the fields of materials, energy, propulsion, operations, procurement and stakeholder engagement. Above all, we need to apply integrated thinking to address these areas not as separate silos but as part of the whole system. We need more awareness that the actions of the industry affect the health of our oceans and have an impact on climate change – and that we all need to work together to find innovative solutions that protect not only the environment but our businesses too.”
The 11th Hour Racing Team’s new IMOCA 60 oozes innovation, thought and attention to detail. It is undoubtedly a high water mark which helps indicate the way to a more sustainable manufacture of performance sailing raceboats, while simultaneously ushering in a new era in IMOCA 60 design – the fully-crewed boat. It will take 11th Hour Racing’s message around the world, and do it at a stylish pace. There is no doubt that change is happening, but the clock is ticking. The slower the industry moves the bigger and more radical the changes will have to be: let’s not leave it past the 11th hour.